The insulation class of a motor refers to a standardized classification system used to specify the thermal capabilities and temperature tolerance of the insulation materials used in the motor’s winding and other components. This classification is essential in determining the safe operating temperature range of the motor under various load conditions. Insulation class information helps engineers and users select the appropriate motor for specific applications to ensure reliability, safety, and longevity.
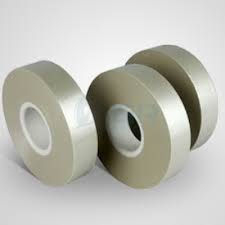
Insulation classes are typically assigned a letter designation, such as Class A, B, F, H, etc. Each class corresponds to a specific maximum allowable temperature rise above the ambient temperature at which the motor can safely operate without damaging the insulation material or reducing the motor’s lifespan. The higher the insulation class, the higher the maximum allowable temperature rise, which indicates better thermal tolerance.
Motor Insulation Classes and Temperature Limits
Insulation Class | Maximum Temperature Rise | Applications |
---|---|---|
Class A (105°C) | 60°C | Low-temperature requirements, light loads |
Class B (130°C) | 75°C | Moderate operating temperatures, moderate loads |
Class F (155°C) | 105°C | Higher thermal endurance, demanding loads |
Class H (180°C) | 125°C | High-temperature applications, heavy-duty operations |
Class N (200°C) | 130°C | Extreme conditions, high-temperature tolerance |
Class R (220°C) | 150°C | Applications demanding high thermal tolerance |
Class S (240°C) | 180°C | Extremely high-temperature requirements |
It’s important to note that while the insulation class indicates the maximum allowable temperature rise, actual operating conditions can impact the motor’s lifespan. Therefore, selecting the appropriate insulation class based on the application’s temperature requirements and load conditions is crucial to ensure reliable and efficient motor performance over time.
The insulation class of an electric motor is decided based on various factors that influence the thermal capabilities and temperature tolerance of the insulation materials used in the motor’s winding and components. The main goal is to ensure that the motor can operate safely and reliably within its intended temperature range. Here are the key factors that contribute to determining the insulation class:
- Temperature Requirements: The primary consideration is the operating temperature requirements of the motor in its intended application. Different industries and applications have varying temperature demands. For instance, industrial motors used in high-temperature environments like steel mills may require higher insulation classes compared to motors used in typical commercial applications.
- Ambient Temperature: The ambient temperature of the environment in which the motor will operate plays a crucial role. The motor’s insulation class should allow it to handle the temperature rise above the ambient temperature without exceeding safe limits. Hot environments will typically require higher insulation classes.
- Duty Cycle: The duty cycle of the motor, which refers to its pattern of operation (continuous, intermittent, or short-term), influences the temperature rise. Motors subjected to continuous or heavy-duty operations may need higher insulation classes to handle prolonged heating.
- Load Conditions: The magnitude and type of load the motor will drive impact its heat generation. Motors driving heavy loads or undergoing frequent start-stop cycles might require higher insulation classes to manage the resulting thermal stress.
- Cooling Method: The cooling method used for the motor, such as natural convection, forced air, or liquid cooling, affects its ability to dissipate heat. Proper cooling helps maintain safe operating temperatures within the insulation class limits.
- Altitude: The altitude at which the motor will operate affects the density of the air and thus the cooling capacity. Higher altitudes result in reduced cooling effectiveness, potentially necessitating a higher insulation class.
- Safety Factors: Insulation classes also consider safety margins to ensure that the motor can handle transient temperature spikes or unusual conditions without risking insulation breakdown.
- Regulatory Standards: Different industries and regions have safety and performance standards that motors must comply with. These standards often prescribe minimum insulation classes based on the motor’s application and environment.
When deciding the insulation class, motor manufacturers consider these factors collectively to ensure that the motor’s insulation system can handle the expected thermal stresses while maintaining safe operating conditions. It’s crucial to select an appropriate insulation class to prevent premature motor failure, overheating, and potential safety hazards. Consulting with motor manufacturers, engineers, or industry standards can help ensure the correct insulation class is chosen for a given application.
Read: